What is laser welding handheld technology and how does it benefit various industries
Laser welding handheld technology is a cutting-edge solution for joining materials with precision using a focused laser beam.

Laser welding handheld technology is a cutting-edge solution for joining materials with precision using a focused laser beam. Unlike traditional welding methods, which often require fixed machines or complex setups, handheld laser welding offers more flexibility and ease of use, making it an ideal choice for a wide range of applications. This technique involves focusing a high-energy laser beam onto the workpieces, which melts the materials at the joint, forming a strong bond once they cool and solidify.
One of the key features of handheld laser welding is its portability. Operators can easily move the handheld laser unit around the workpiece, providing more versatility compared to fixed laser systems or traditional welding machines. This is particularly advantageous in industries where access to the welding site is challenging or where there is a need for intricate or detailed welds in hard-to-reach areas.
Handheld laser welding technology is based on the principles of laser beam generation and the process of focused energy transfer. The laser beam is typically generated by a fiber laser or a diode laser, which produces a concentrated beam of light that can be directed with high precision. When the beam is directed onto the material, it heats up the surface and causes it to melt. The energy is precisely controlled, allowing for the creation of high-quality welds with minimal heat-affected zones (HAZ).
Benefits for Various Industries:
-
Precision and Quality: Laser welding handheld units offer exceptional precision, making them suitable for high-accuracy applications. The laser beam can be finely adjusted to create narrow, deep welds, which is essential in industries where product quality is critical, such as electronics, medical devices, and aerospace. The low heat input also reduces the chances of warping or distortion, ensuring a cleaner weld with less post-processing required.
-
Versatility: The handheld nature of the laser welding tool allows operators to work on a variety of materials and workpieces of different sizes and shapes. This versatility is especially beneficial in industries like automotive repair, construction, and manufacturing, where workers may need to weld complex parts or work in confined spaces. Handheld laser welders can effectively weld metals such as stainless steel, aluminum, titanium, and copper, expanding their applications across a wide range of sectors.
-
Speed and Efficiency: Laser welding is known for its speed and efficiency. Unlike traditional welding methods, which may require multiple passes or slow cooling times, laser welding can create strong, clean welds in a matter of seconds. The rapid process significantly reduces production time, making it ideal for industries focused on high-volume manufacturing, such as automotive and electronics production.
-
Minimal Heat-Affected Zone (HAZ): One of the major advantages of laser welding is its ability to minimize the heat-affected zone (HAZ), the area of the workpiece that undergoes a significant change in temperature and structure due to the welding process. The smaller HAZ ensures that surrounding materials are not adversely affected by heat, preventing distortion or weakening of the surrounding material. This is especially important in industries like aerospace, where maintaining the integrity of the material is crucial.
-
Reduced Need for Consumables and Maintenance: Handheld laser welders require fewer consumables compared to traditional welding methods. There is no need for filler materials in many cases, which reduces both costs and environmental impact. Furthermore, laser systems typically require less maintenance because they do not rely on contact parts that wear out over time, making them more durable and cost-effective in the long run.
-
Minimal Post-Processing: Since laser welding results in cleaner and more precise welds, the need for post-weld processing (such as grinding, polishing, or cleaning) is significantly reduced. This makes it a time-efficient solution for industries where minimizing additional processing steps is important, such as in the production of precision components.
Conclusion:
Handheld laser welding technology represents a significant advancement in the field of welding, offering advantages in precision, versatility, speed, and efficiency. Its portability and ability to create high-quality welds with minimal heat impact make it a valuable tool for a wide range of industries, from automotive and aerospace to electronics and medical devices. As the technology continues to evolve, it is expected that handheld laser welding will become even more accessible and cost-effective, further transforming manufacturing processes and improving product quality across various sectors.
What's Your Reaction?


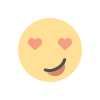



